From simulation to automation, digital tools enable aerospace manufacturers’ move from reactive to proactive quality strategy.
Hexagon has sponsored this post.
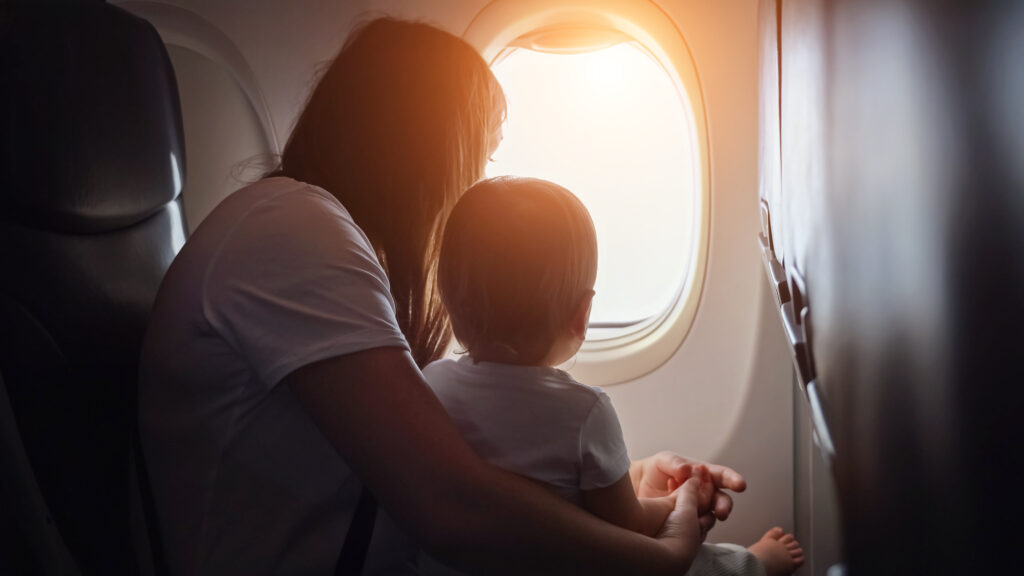
In aviation, quality is synonymous with safety — there’s no room for error. Every component that goes into an aircraft must meet strict performance, manufacturing and certification requirements in order to assure airworthiness. But maintaining that level of consistency is no small feat in an industry where complex global supply chains and shifting workforces create countless opportunities for deviation.
“Today, up to 30% of the total manufacturing cost comes from quality-related processes—scrap and rework, supply chain disruptions, inspections and delays,” says Aziz Tahiri, VP of Global Aerospace & Defense at Hexagon. “We know ramp-up is needed, but many are still stuck in reactive mode, and the cost is simply too high. To become proactive, we must digitize inspection, supervise it intelligently and give everyone better ways to interpret and act on the data. That requires both new technologies and new workflows.”
As designs evolve from CAD models to manufactured parts, aerospace companies must build quality into every step — and that’s where data and digital tools come in.
Better quality starts with better data
Aerospace supply chains are vast and fragmented, often with limited data-sharing making it difficult to trace every component’s journey throughout its lifecycle. This lack of visibility can lead to undetected issues that surface too late in the production process, driving up scrap rates.
“Are we losing money because the raw materials are not there, the wrong people are there or the supply chain is supplying parts with a delay?” says Tahiri. “Is it a process question? Engineers need a better understanding of where the non-quality costs are, to be able to run targeted optimization of a factory.”
To improve quality, engineers need contextualized data: who operated the machine, when it was last calibrated, under what conditions the measurement took place. Just as important is the accuracy of the measurement, as well as a well-defined reference against which to evaluate the part or process.
Capturing data isn’t enough; it also matters when it’s captured. In-process inspection — checking parts at various manufacturing milestones — allows teams to catch problems closer to their source. “If you’re only measuring at the end of the production cycle, finding the root cause of a quality issue is very complicated,” explains Tahiri. “You don’t know if it happened at step one of the production process or step ten. Is it the machine? Is it the operator? Is it the program? Is it the temperature? You don’t know — there are so many options.”
Turning data into quality optimization with digital tools
Once contextualized data is collected, it can feed into digital tools to help aviation shift from reactive to proactive decision-making. Simulation, for example, helps engineers improve quality outcomes by allowing them to test what-if scenarios without interrupting production — whether it’s adjusting a machine program or modifying how a part is fixtured.
“Simulation is now so high fidelity, it’s 99% representative of what will happen in reality,” says Tahiri. “Instead of halting production to try a fix that might not work and potentially causing damage to the parts and your machines, you can test it virtually, with confidence that when you apply it, it will deliver.”
Artificial intelligence and machine learning (AI/ML) further accelerates processes by quickly analyzing massive datasets, identifying trends, and recommending solutions. Industrial Internet of Things (IIoT) and cloud platforms make it easier to share data across departments, enabling traceability and collaboration to solve issues more efficiently.
Finally, automation not only speeds up repetitive inspection tasks — it can also strengthen the feedback loop between digital design and physical manufacturing. “Once you have a feedback loop in action, you want to automate it and let it run on its own,” explains Tahiri. “The more you reduce the gap between design intent and manufactured part, the more you’re optimizing your productivity and quality.”
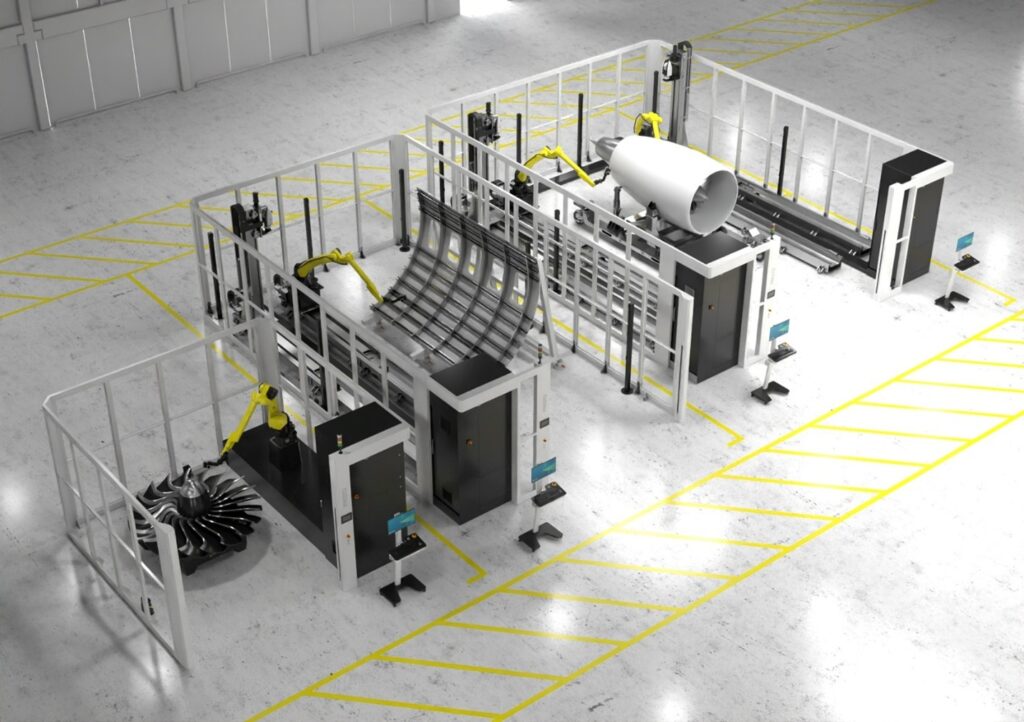
Building a safer future
Hexagon offers a combination of advanced measurement systems and digital tools to help aviation companies embed quality into every stage of production. The company’s portfolio includes ultra-precise, contactless laser scanning systems for measuring parts of all sizes, from small electronic components to full aircraft structures. Its simulation software models product physics and manufacturing processes ranging from 3D printing to metal forming and CNC machining.
In aerospace, where every micron matters and delays can cost millions, isolated tools and fragmented workflows are no longer sustainable. From initial design to final inspection, success depends on seamless coordination, instant feedback and unified data. The ability to connect every stage of production — from simulation to manufacturing to quality control — isn’t just a competitive edge anymore; it’s inevitable.
That’s why data plays a pivotal role. When it’s contextualized, accessible and shared in real time across functions, it becomes the glue that holds the entire production lifecycle together. From design engineers to inspection teams, everyone operates with the same clarity and confidence.
Hexagon makes this possible with Nexus, its powerful digital reality platform that connects teams, tools and workflows across the entire manufacturing chain. With Nexus, deviations are caught earlier, decisions are made faster and quality is embedded into every step — accelerating innovation while reducing risk.
“Ultimately, it’s not just about technology — it’s about empowering people to make better decisions with better data,” says Tahiri. “When quality becomes intuitive and proactive, we’re not only improving production — we’re protecting lives. That’s what we mean when we say ‘quality for life.’”
To learn more about how to achieve “right-first-time” manufacturing to minimize waste and rework or how automation and AI-driven inspection can enhance precision and efficiency in aerospace & defence, visit Hexagon – Embedding quality in aerospace.