Looking back on the Additive Manufacturing Users Group Conference for 2025.
It’s been several weeks since I attended my first Additive Manufacturing Users Group (AMUG) Conference in Chicago, but my head is still spinning. Not so much from the food and drink and company (though all three were excellent) but from the sheer volume of information there was to take in from the very beginning.
Anyone who’s attended a conference or tradeshow knows that it can feel – as our own Jim Anderton has put it – like drinking from a firehose. For a journalist who relies on subject matter experts, these kinds of events offer the chance to speak to and hear from so many at one time in one place that their value is practically incalculable (travel expenses notwithstanding).
The AMUG difference
What makes AMUG special is the opportunity to get insights and perspectives from both 30,000 feet and at the ground level, sometimes in the same discussion or presentation. That was demonstrated in the Diamond Sponsor Panel on the first full day, which included representatives from DMG Mori, GoEngineer, SME, Stratasys, and Würth Additive Group. The discussion covered everything from broad market and tech trends, to specific automotive and defense applications, to particular barriers to entry for new users.
“AMUG’s a different show than any other,” said AJ Strandquist, CEO of Würth Additive Group. “It’s the only one where people are encouraged to teach rather than sell [and] there’s probably not a bigger collection of collective experience in this industry.”
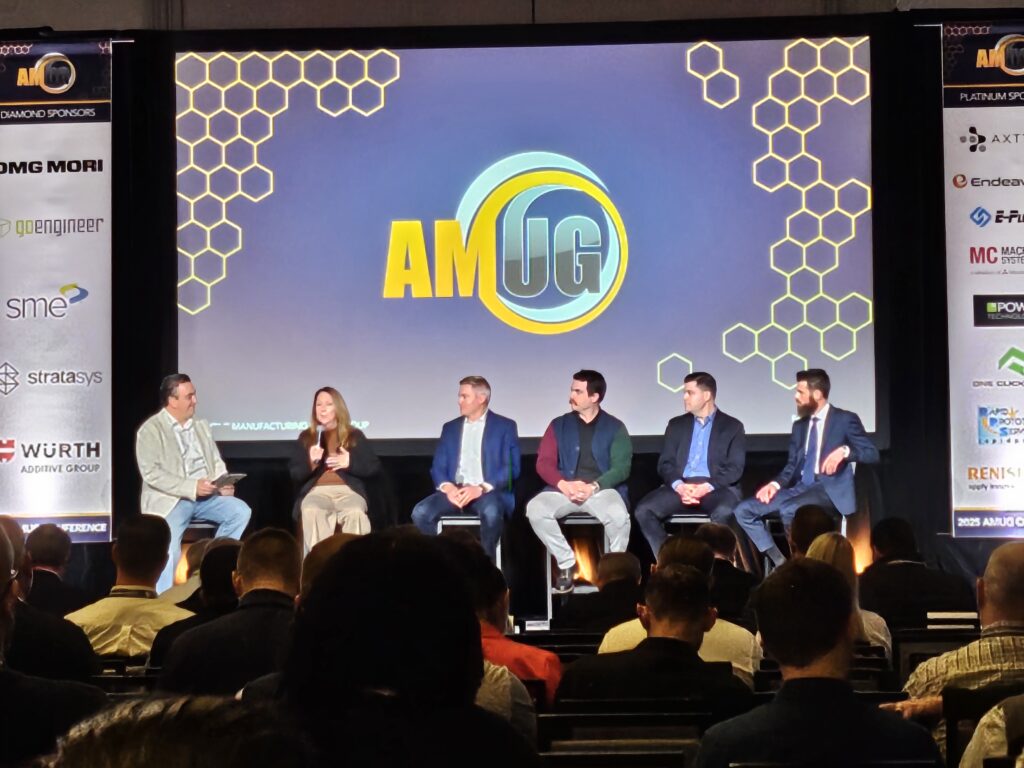
The collective industry experience at AMUG is personified by Joe Allison, winner of the 2025 Innovators Award. Allison began his career in 3D printing as an engineer at 3D Systems, joining the company just a few short weeks after encountering stereolithography for the first time at a trade show in 1987. Since then, his long list of accomplishments in the industry has included co-founding Solid Concepts (which became part of Stratasys Direct Manufacturing), working as an EVP at Stratasys, serving as CEO for Evolve Additive Solutions and, most recently, as the CEO for Gentle Giant Studios.
With a history nearly as old as the 3D printing industry itself, Allison is uniquely positioned to comment on where it stands today. In a fireside chat at AMUG, he said:
“We’ve seen a few bubbles over the years – where stock prices skyrocket, lots of money flows into startups, and everyone’s excited. But the reality is: most startups fail. When the market corrects, valuations collapse and the money dries up, many companies – some of which were actually decent businesses – just don’t have enough runway to survive.
“In the long run though, the industry always recovers: new companies emerge, a decade goes by and people forget, and we start again. I agree that we’ve largely tapped out the prototyping market, but that’s a good thing. Prototyping gave us a launchpad to develop the technology. Now it’s about transitioning into end-use, production-scale applications; and that transition will take years.”
AMUG in session(s)
I’d heard a lot about how the breakout sessions at AMUG were different from those at other tradeshows and conferences, the latter often revealing themselves to be little more than thinly disguised sales pitches. My assumption was that this meant I should expect sessions like those from the academic conferences I’d attended as a grad student, but that wasn’t quite right either.
While there were the usual case study presentations and panel discussions on industry trends, there was also “Snap, Crack & Pop: Hands-on Material Testing”, which had the longest line-up I’ve ever seen at a professional event. The idea for it was simple but compelling, particularly for engineers who enjoy watching things break. The session involved several different stations showcasing the effects of various mechanical and thermal stresses on different 3D printed polymers.
Particular standouts from this session included hotdogs cooking in a pan made from Ultem 1010 on a hotplate and a set of 3D printed dentures attached to a vise, which served as a simulated jaw that was continuously fed jawbreakers.
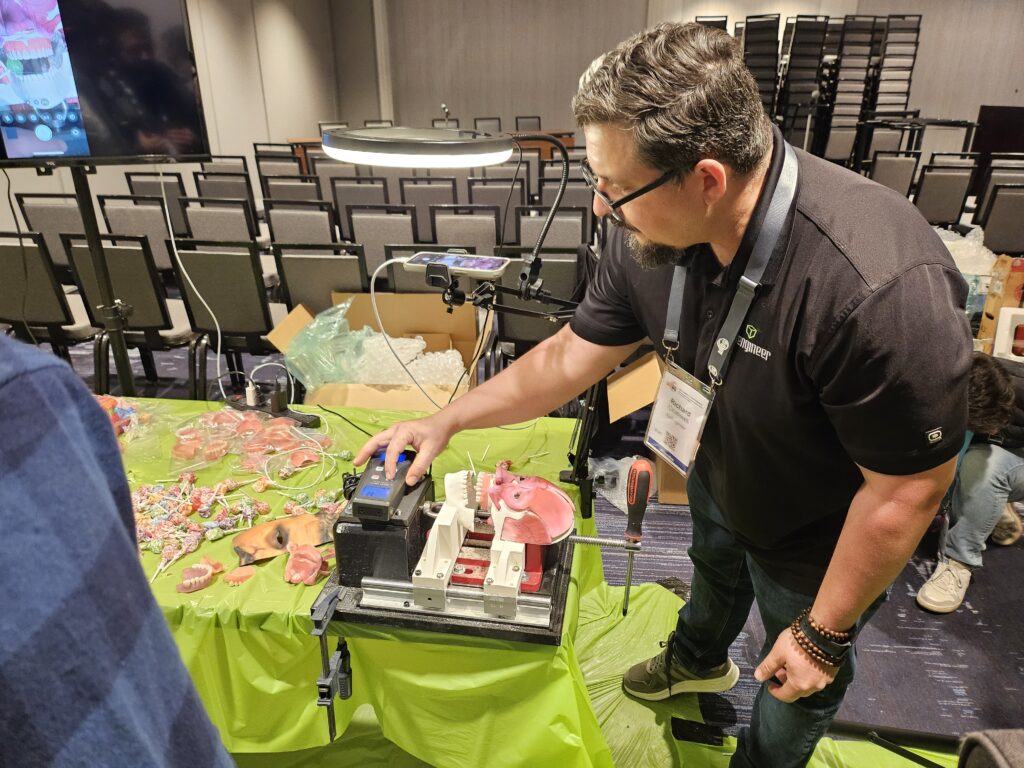
“I really wanted people to experience the materials, because a datasheet can only take you so far,” explained Heather Natal from GoEngineer, who came up with the idea for the unique session. “This gives them an opportunity to see real-life examples of how each material can stand up to different elements, such as heat or pressure or torquing. My son was having a science fair, which gave me the idea for having different stations.”
Another session that stood out to me was a workshop entitled “DFAM Problem Solving for Legacy Components” organized by Endeavor 3D. As a contract manufacturer, Endeavor 3D is well acquainted with requests to produce legacy parts using additive technologies – in this particular case, the focus was on MultiJet Fusion (MJF). Two of the company’s engineers gave a short presentation with an overview of design for additive manufacturing (DFAM) and designing for MJF in particular before splitting the attendees into groups and presenting them with three exercises based on real-world use cases.
After introducing myself as a journalist and apologizing in advance for being woefully underqualified to contribute, I sat back and watched my group design a beer tap, the interior cavity of a small wing, and finally a drone body. In each exercise, the group discussed how best to take advantage of MJF technology, debating lattice designs, discussing possibilities for topology optimization, and introducing sacrificial augers to help with powder removal. Watching these engineers at work gave me a new appreciation for just how much 3D printing can open the design space, even for legacy products.
I hope it did for them as well.
Final thoughts
The last day of the event opened with a keynote from Joe Scarbo, a mechanical engineer and founder of Scarbo Performance. Though he started by apologizing for his lack of public speaking skills, Scarbo’s passion for automotive engineering shone through whenever the subject turned to the vehicles he and his team have built.
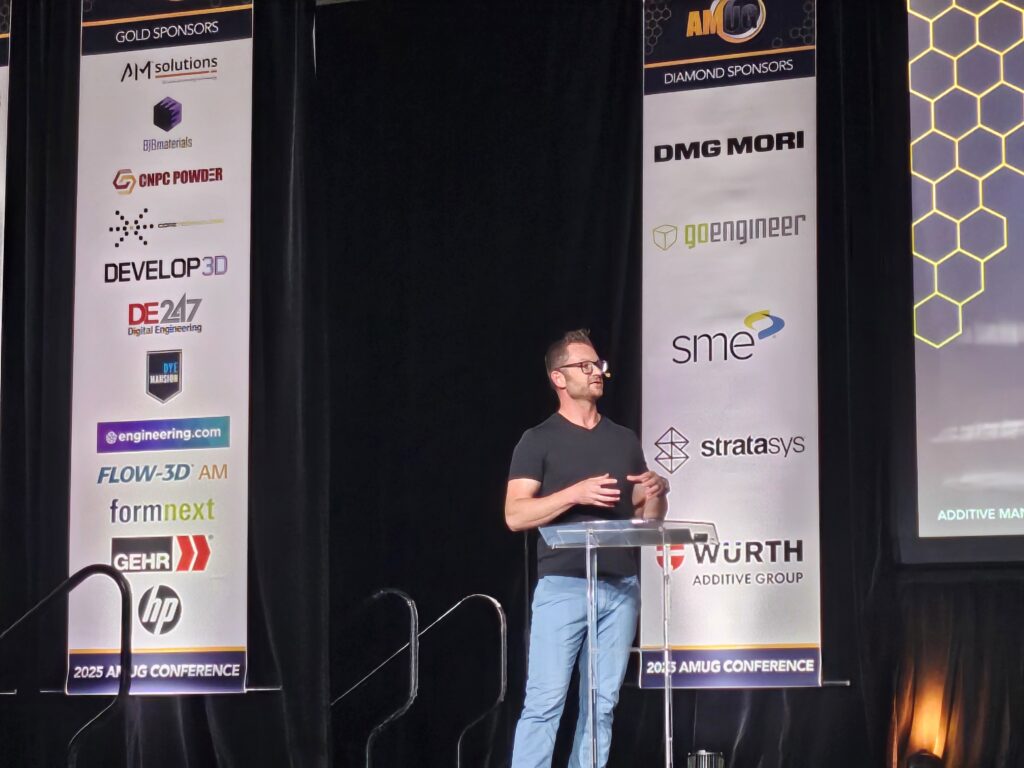
Scarbo was a fitting choice as a keynote speaker for AMUG. He’s an additive manufacturing user who sees 3D printing for what it is: a specialized tool that can be incredibly powerful when utilized correctly.
“Additive has come very far in the past few years,” he said in his closing remarks. “The part quality and the material properties are so good now that I no longer think of it as just a rapid prototyping solution. It’s an end-use solution for us.”
There’s much more that I could (and will) write about this year’s AMUG: the case studies in aerospace, defense and infrastructure; the tips and tricks for getting the most out of 3D printing software and hardware; the winners of the technical competition; the NASA engineer using AM to bring samples back from Mars.
Suffice to say, if you’re passionate about additive manufacturing, there’s no better place to be than AMUG.